Amazon has acquired the AI wearables startup Bee, which makes a bracelet and an Apple Watch app that record your day-to-day life to function as an AI assistant.
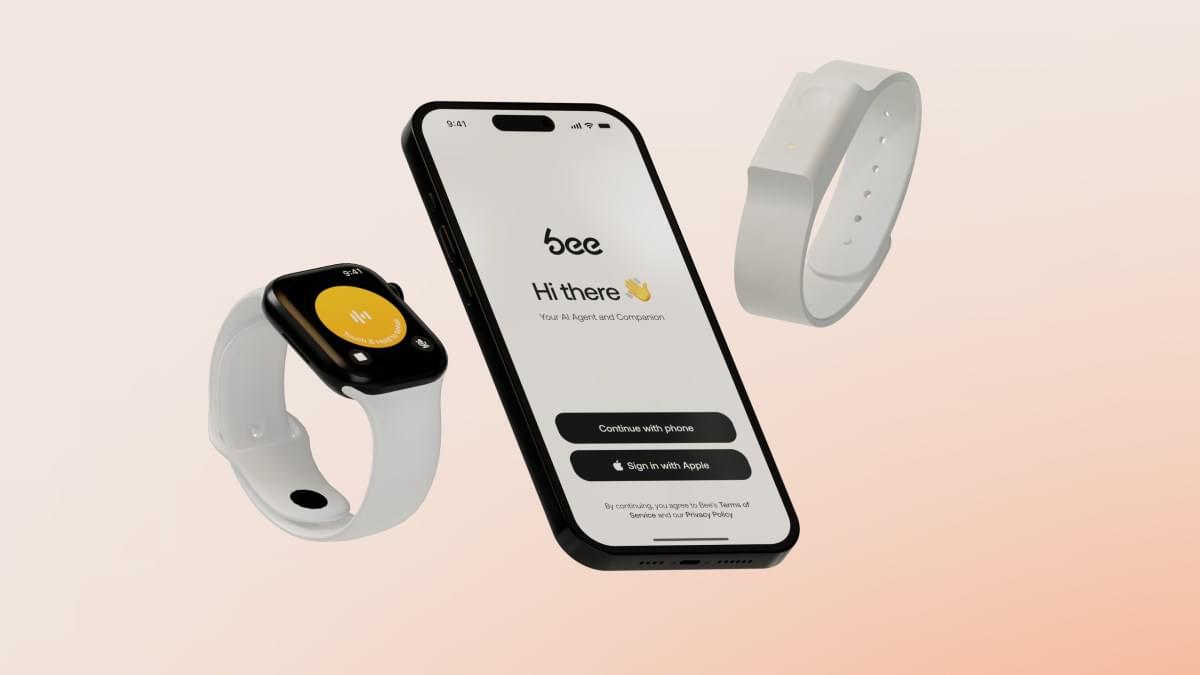
The development of wearable electronics and the current era of big data requires the sustainable power supply of numerous distributed sensors. In this paper, we designed and experimentally studied an energy harvester based on ferrofluid sloshing. The harvester contains a horizontally positioned cylindrical vial, half-filled with a ferrofluid exposed to a magnetic field. The vial is excited by a laboratory shaker and the induced voltage in a nearby coil is measured under increasing and decreasing shaking rates. Five ferrofluid samples are involved in the study, yielding the dependence of the electromotive force on the ferrofluid magnetization of saturation. The energy harvesting by ferrofluid sloshing is investigated in various magnetic field configurations. It is found that the most effective magnetic field configuration for the energy harvesting is characterized by the field intensity perpendicular to the axis of the vial motion and gravity. The harvested electric power linearly increases with the ferrofluid magnetization of saturation. The electromotive force generated by each ferrofluid is found identical for measurements in acceleration and deceleration mode. A significant reduction in the induced voltage is observed in a stronger magnetic field. The magneto-viscous effect and partial immobilization of the ferrofluid in the stronger magnetic field is considered. The magneto-viscous effect is documented by a supplementing experiment. The results extend knowledge on energy harvesting by ferrofluid sloshing and may pave the way to applications of ferrofluid energy harvesters for mechanical excitations with changing directions in regard to the magnetic field induction.
Rajnak, M., Kurimsky, J., Paulovicova, K. et al. Vibration energy harvesting by ferrofluids in external magnetic fields. Sci Rep 15, 26,701 (2025). https://doi.org/10.1038/s41598-025-12490-w.
Dr. Jung-Dae Kwon’s research team at the Energy & Environmental Materials Research Division of the Korea Institute of Materials Science (KIMS) has successfully developed an amorphous silicon optoelectronic device with minimal defects, even using a low-temperature process at 90°C. The findings are published in the journal Advanced Science.
Notably, the team overcame the limitations of high-temperature processing by precisely controlling the hydrogen dilution ratio—the ratio of hydrogen to silane (SiH4) gas—enabling the fabrication of high-performance flexible optoelectronic devices (sensors that detect light and convert it into electrical signals).
Flexible optoelectronic devices are key components of next-generation electronic devices, such as wearable electronics and image sensors, and require the precise deposition of thin films on thin, bendable substrates. However, a major limitation has been the necessity of high-temperature processing above 250°C, making it difficult to apply these devices to heat-sensitive flexible substrates.
School of Physics Associate Professor Elisabetta Matsumoto is unearthing the secrets of the centuries-old practice of knitting through experiments, models, and simulations. Her goal? Leveraging knitting for breakthroughs in advanced manufacturing—including more sustainable textiles, wearable electronics, and soft robotics.
Matsumoto, who is also a principal investigator at the International Institute for Sustainability with Knotted Chiral Meta Matter (WPI-SKCM2) at Hiroshima University, is the corresponding author on a new study exploring the physics of ‘jamming’—a phenomenon when soft or stretchy materials become rigid under low stress but soften under higher tension.
The study, “Pulling Apart the Mechanisms That Lead to Jammed Knitted Fabrics,” is published in Physical Review E, and also includes Georgia Tech Matsumoto Group graduate students Sarah Gonzalez and Alexander Cachine in addition to former postdoctoral fellow Michael Dimitriyev, who is now an assistant professor at Texas A&M University.
Could clothing monitor a person’s health in real time, because the clothing itself would be a self-powered sensor? A new material created through electrospinning, which is a process that draws out fibers using electricity, brings this possibility one step closer.
A team led by researchers at Penn State has developed a new fabrication approach that optimizes the internal structure of electrospun fibers to improve their performance in electronic applications. The team has published its findings in the Journal of Applied Physics.
This novel electrospinning approach could open the door to more efficient, flexible and scalable electronics for wearable sensors, health monitoring and sustainable energy harvesting, according to Guanchun Rui, a visiting postdoctoral student in the Department of Electrical Engineering and the Materials Research Institute and co-lead author of the study.
USC scientists have developed a wearable system that enables more natural and emotionally engaging interactions in shared digital spaces, opening new possibilities for remote work, education, health care and beyond.
Touch plays a vital role in how humans communicate and bond. From infancy through adulthood, physical contact helps foster emotional bonds, build trust and regulate stress. Yet in today’s increasingly digital world, where screens mediate many of our relationships, it is often missing.
To bridge the gap, researchers at the USC Viterbi School of Engineering have developed a wearable haptic system that lets users exchange physical gestures in virtual reality and feel them in real time, even when they’re miles apart. Their paper is published on the arXiv preprint server.
Although lithium is highly effective in treating bipolar disorder, the chemical has a narrow therapeutic window—too high a dose can be toxic to patients, causing kidney damage, thyroid damage, or even death, while too low a dose renders the treatment ineffective.
The dose of lithium varies between individuals based on body weight, diet, and other physiological factors, and requires regular measurement of lithium levels in the blood. Currently, this is only available through standard laboratory-based blood draws, which can be time-consuming, inconvenient, and painful. This makes personalized and easily-accessible lithium monitoring an important goal in the treatment for bipolar disorder.
“Our goal was to create an easy-to-use sensor that bypasses the need for blood draws entirely,” explained Yasser Khan, a USC Ming Hsieh Department of Electrical and Computer Engineering professor who leads the USC Khan Lab, and part of the USC Institute for Technology and Medical Systems (ITEMS), a joint initiative of USC Viterbi School of Engineering and Keck School of Medicine of USC focusing on innovative medical devices.
Precision and personalized medicine for disease management necessitates real-time, continuous monitoring of biomarkers and therapeutic drugs to adjust treatment regimens based on individual patient responses. This study introduces a wearable Microneedle-based Continuous Biomarker/Drug Monitoring (MCBM) system, designed for the simultaneous, in vivo pharmacokinetic and pharmacodynamic evaluation for diabetes. Utilizing a dual-sensor microneedle and a layer-by-layer nanoenzyme immobilization strategy, the MCBM system achieves high sensitivity and specificity in measuring glucose and metformin concentrations in skin interstitial fluid (ISF). Seamless integration with a smartphone application enables real-time data analysis and feedback, fostering a pharmacologically informed approach to diabetes management. The MCBM system’s validation and in vivo trials demonstrate its precise monitoring of glucose and metformin, offering a tool for personalized treatment adjustments. Its proven biocompatibility and safety suit long-term usage. This system advances personalized diabetes care, highlighting the move towards wearables that adjust drug dosages in real-time, enhancing precision and personalized medicine.
Real-time monitoring of drugs and biomarkers is essential for personalized diabetes care. Here, the authors present a wearable microneedle sensor system enabling simultaneous in vivo monitoring of glucose and metformin in interstitial fluids for personalized medicine.