A study published in Physical Review Letters (PRL) details a “Gambling Carnot Engine” that researchers report can attain 100% efficiency while also improving power generation.
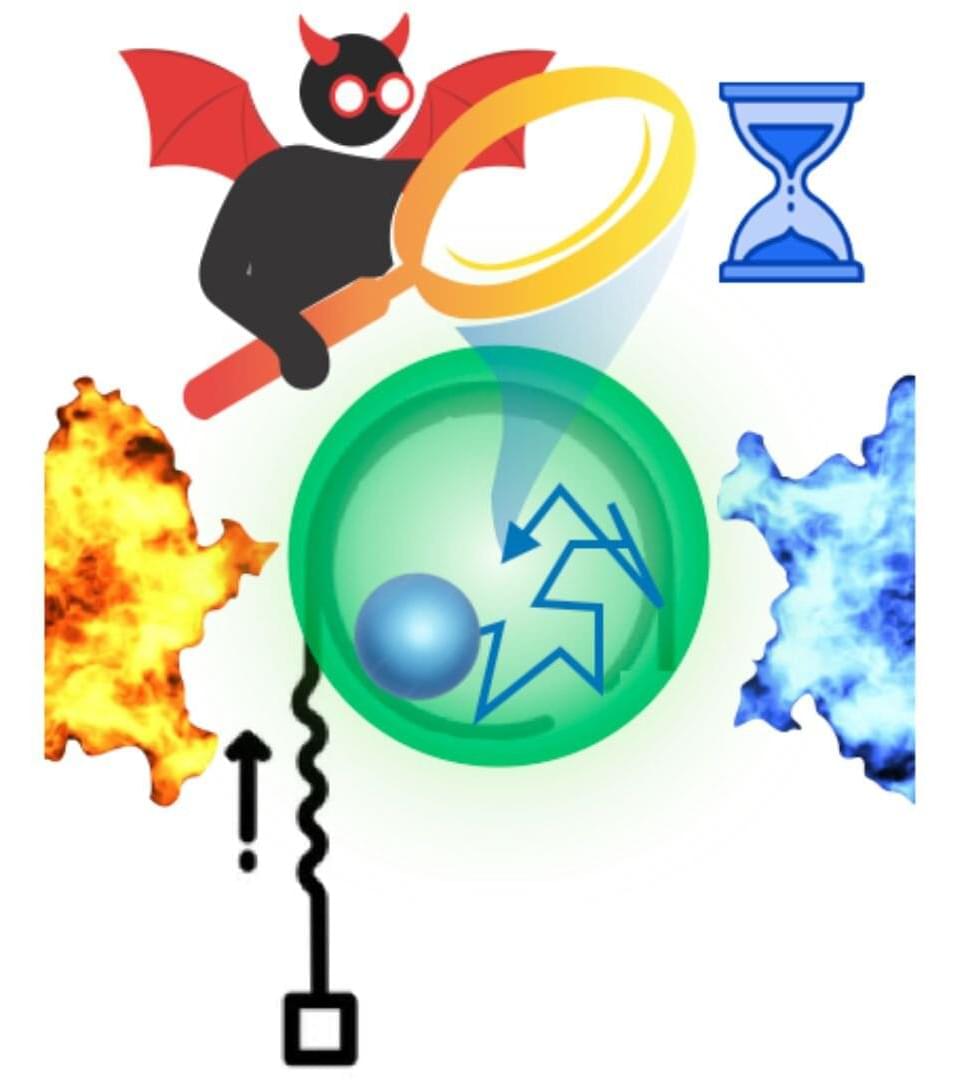
University at Albany chemists have created a new high-energy compound that could revolutionize rocket fuel and make space flights more efficient. Upon ignition, the compound releases more energy relative to its weight and volume compared to current fuels. In a rocket, this would mean less fuel required to power the same flight duration or payload and more room for mission-critical supplies. Their study is published in the Journal of the American Chemical Society.
“In rocket ships, space is at a premium,” said Assistant Professor of Chemistry Michael Yeung, whose lab led the work. “Every inch must be packed efficiently, and everything onboard needs to be as light as possible. Creating more efficient fuel using our new compound would mean less space is needed for fuel storage, freeing up room for equipment, including instruments used for research. On the return voyage, this could mean more space is available to bring samples home.”
The newly synthesized compound, manganese diboride (MnB2), is over 20% more energetic by weight and about 150% more energetic by volume compared to the aluminum currently used in solid rocket boosters. Despite being highly energetic, it is also very safe and will only combust when it meets an ignition agent like kerosene.
Researchers in Germany have unveiled the Metafiber, a breakthrough device that allows ultra-precise, rapid, and compact control of light focus directly within an optical fiber. Unlike traditional systems that rely on bulky moving parts, the Metafiber uses a tiny 3D nanoprinted hologram on a dual-core fiber to steer light by adjusting power between its cores. This enables seamless, continuous focus shifts over microns with excellent beam quality.
From precision machining to advanced microscopy, the demand for higher-power, ultrafast lasers continues to grow. Traditionally, researchers have relied on single-mode fibers to build these lasers, but they face a fundamental physical limit on energy output. To break through this bottleneck, we have turned to multimode fibers, which can carry many light modes—essentially different shapes of light—at once, a technique known as spatiotemporal mode-locking (STML).
However, getting these different modes to work together in harmony has been a significant challenge. In our latest research, published in Optics Letters, we have developed a new technique that allows us to precisely and independently control each of these transverse modes, leading to a dramatic boost in laser power and versatility.
The core problem we faced is known as intermodal dispersion. In a multimode fiber, different light modes travel at slightly different speeds. This velocity mismatch causes the laser pulses to spread out and separate in time and space, preventing the formation of stable, high-power pulses. Previous STML techniques typically used a method called spatial filtering to compensate for this dispersion, but this approach limits the number of modes that can be locked together, thereby capping the potential power enhancement.
The University of Jyväskylä, Finland, has been involved as part of an international collaboration that has identified a way to completely suppress superconductivity in superconducting and ferromagnetic junctions. The results published in Nature Communications are key to the development of non-volatile superconducting random access memories and could enable more energy-efficient information and communication technologies.
The pursuit of more efficient engines continually pushes the boundaries of thermodynamics, and recent work demonstrates that relativistic effects may offer a surprising pathway to surpass conventional limits. Tanmoy Pandit from the Leibniz Institute of Hannover, along with Tanmoy Pandit from TU Berlin and Pritam Chattopadhyay from the Weizmann Institute of Science, and colleagues, investigate a novel thermal machine that harnesses the principles of relativity to achieve efficiencies beyond those dictated by the Carnot cycle. Their research reveals that by incorporating relativistic motion into the system, specifically through the reshaping of energy spectra via the Doppler effect, it becomes possible to extract useful work even without a temperature difference, effectively establishing relativistic motion as a valuable resource for energy conversion. This discovery not only challenges established thermodynamic boundaries, but also opens exciting possibilities for designing future technologies that leverage the fundamental principles of relativity to enhance performance.
The appendices detail the Lindblad superoperator used to describe the system’s dynamics and the transformation to a rotating frame to simplify the analysis. They show how relativistic motion affects the average number of quanta in the reservoir and the superoperators, and present the detailed derivation of the steady-state density matrix elements for the three-level heat engine, providing equations for power output and efficiency. The document describes the Monte Carlo method used to estimate the generalized Carnot-like efficiency bound in relativistic quantum thermal machines, providing pseudocode for implementation and explaining how the efficiency bound is extracted from efficiency and power pairs. Overall, this is an excellent supplementary material document that provides a comprehensive and detailed explanation of the theoretical framework, calculations, and numerical methods used in the research paper. The clear organization, detailed derivations, and well-explained physical concepts make it a valuable resource for anyone interested in relativistic quantum thermal machines.
Relativistic Motion Boosts Heat Engine Efficiency
Researchers have demonstrated that relativistic motion can function as a genuine thermodynamic resource, enabling a heat engine to surpass the conventional limits of efficiency. The team investigated a three-level maser, where thermal reservoirs are in constant relativistic motion relative to the working medium, using a model that accurately captures the effects of relativistic motion on energy transfer. The results reveal that the engine’s performance is not solely dictated by temperature differences, but is significantly influenced by the velocity of the thermal reservoirs. Specifically, the engine can operate with greater efficiency than predicted by the Carnot limit, due to the reshaping of the energy spectrum caused by relativistic motion.
Compared with the energy-intensive Haber-Bosch process, renewable energy-driven electrocatalytic nitrate reduction reaction (NO3−RR) provides a low-carbon route for ammonia synthesis under mild conditions. Using nitrate from wastewater as the nitrogen source and water as the hydrogen source, this route has the potential to produce ammonia sustainably while mitigating water pollution.
Copper (Cu)-based catalysts show a good performance for NO3−RR to ammonia. However, they suffer from issues including high overpotential, competing nitrite (NO2–) formation, and low overall energy efficiency.
In a study published in ACS Catalysis, a team led by Prof. Bao Xinhe and Prof. Gao Dunfeng from the Dalian Institute of Chemical Physics (DICP) of the Chinese Academy of Sciences, along with Prof. Wang Guoxiong from Fudan University, proposed hydroxyl (*OH) adsorption as a selectivity descriptor for ammonia synthesis via NO3−RR over Cu catalysts.