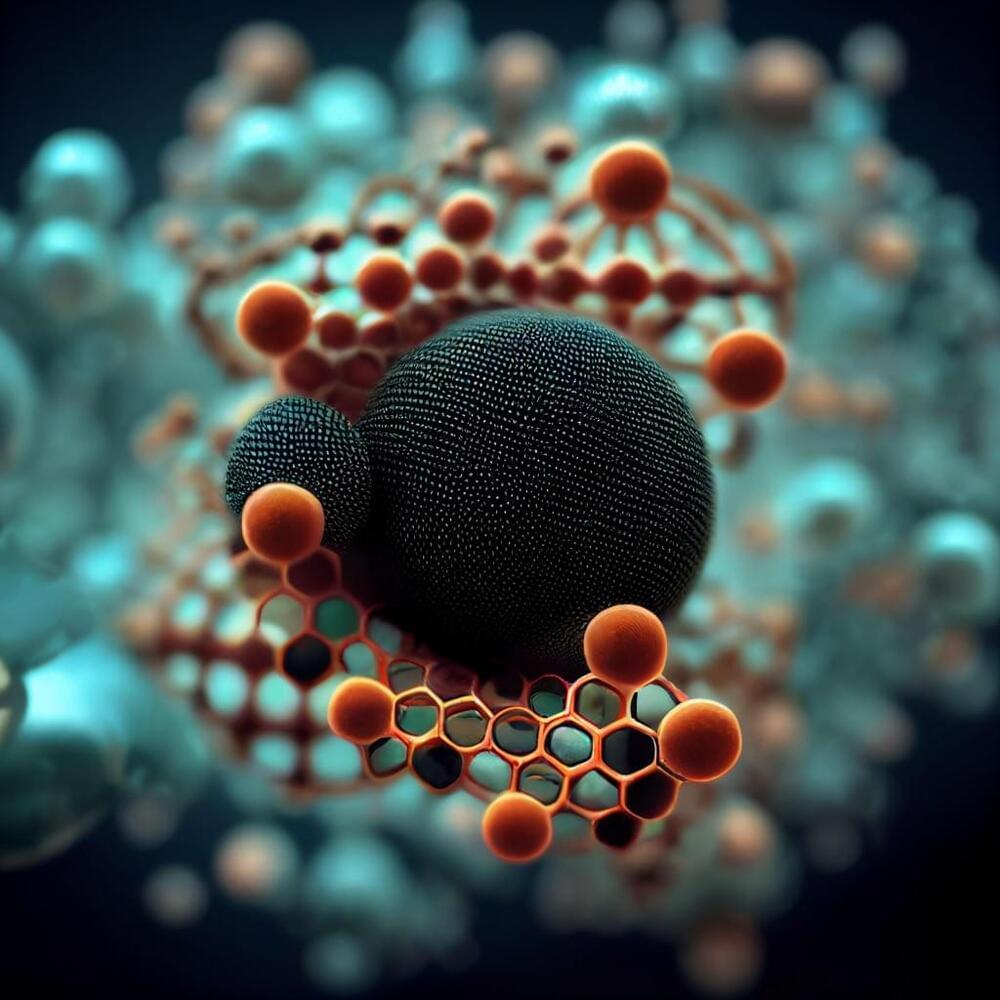
Lipid nanoparticles (LNPs) transport small molecules into the body. The most well-known LNP cargo is mRNA, the key constituent of some of the early vaccines against COVID-19. But that is just one application: LNPs can carry many different types of payload, and have applications beyond vaccines.
Barbara Mui has been working on LNPs (and their predecessors, liposomes) since she was a PhD student in Pieter Cullis’s group in the 1990s. “In those days, LNPs encapsulated anti-cancer drugs,” says Mui, who is currently a senior scientist at Acuitas, the company that developed the LNPs used in the Pfizer-BioNTech mRNA vaccine against SARS-CoV-2. She says it soon became clear that LNPs worked even better as carriers of polynucleotides. “The first one that worked really well was encapsulating small RNAs,” Mui recalls.
But it was mRNA where LNPs proved most effective, primarily because LNPs are comprised of positively charged lipid nanoparticles that encapsulate negatively charged mRNA. Once in the body, LNPs enter cells via endocytosis into endosomes and are released into the cytoplasm. “Without the specially designed chemistry, the LNP and mRNA would be degraded in the endosome,” says Kathryn Whitehead, professor in the departments of chemical engineering and biomedical engineering at Carnegie Mellon University.