A radical redesign of commercial aircraft, called the flying-V plane, could increase fuel efficiency by 20%, greatly reducing emissions.
Category: energy – Page 106
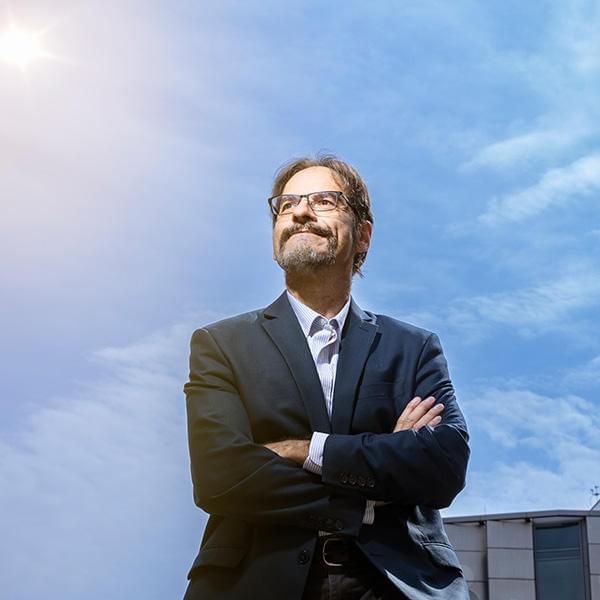
Mason scientists to work with the U.S. Navy to avert ‘internet apocalypse’
A team of George Mason University scientists has received a federal grant of more than $13 million to work with the Department of the Navy to study and better understand increased solar activity that could potentially cause an “internet apocalypse” disrupting all electronic communications on Earth, including satellite communications.
Research from the grant, which will total $13.6 million in expenditures over five years, will be done in collaboration with the Naval Research Laboratory (NRL), and will include state-of-the-art data mining, analysis, and scientific modeling, among other endeavors, led by Mason faculty, students and staff. Under the terms of the contract, Mason provides scientific support for a broad range of astronomy-related activities that are of interest to the U.S. Navy and the nation at large.
“The main focus is on solar activity and the way it can impact systems on Earth,” said principal investigator Peter A. Becker, a professor in the Department of Physics and Astronomy within the College of Science. “This is especially important to the Navy—and more broadly the Department of Defense—because high-energy outbursts from the sun can have a strong negative impact on earthly radio and internet communications. And they can also have a detrimental effect on navigation systems and energy grids on Earth.”
How Einstein Unlocked the Quantum Universe and Created the Photon
It started with a simple experiment that was all the rage in the early 20th century. And as is usually the case, simple experiments often go on to change the world, leading Einstein himself to open the revolutionary door to the quantum world.
Here’s the setup. You take a piece of metal. You shine a light on it. You wait for the electrons in the metal to get enough energy from the light that they pop off the surface and go flying out. You point some electron-detector at the metal to measure the number and energy of the electrons.
Done.

Polestar 5 to showcase StoreDot’s ultra fast-charging technology
Extreme fast charging (XFC) battery technology
StoreDot is a leader in extreme fast charging (XFC) battery technology, which uses silicon-dominant chemistries to enable rapid charging without compromising energy density or safety. The company has successfully validated its “100in5” XFC cell, which can deliver 100 miles of range in five minutes, at an independent battery lab in Israel. The cell has also shown superior performance compared to other EV batteries.
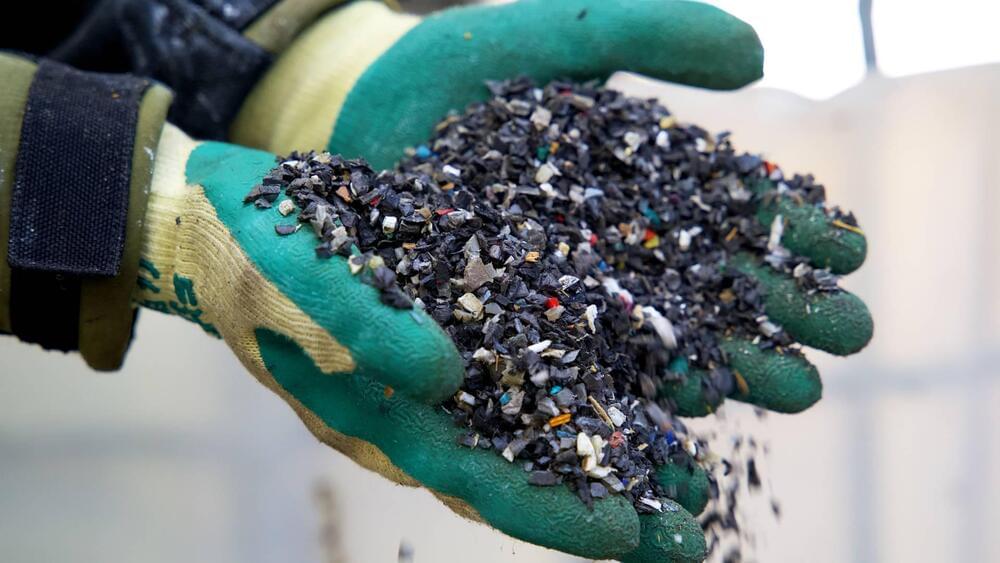
At least 491 dangerous chemicals found in recycled plastics
“Plastic recycling has been touted as a solution to the plastics pollution crisis, but toxic chemicals in plastics complicate their reuse and disposal and hinder recycling.”
As such, plastic recycling today is an essential part of waste management and environmental preservation initiatives. Recycling plastics minimizes the environmental impact of plastic manufacturing, conserves energy, and helps lower the need for new raw materials.
A crucial sustainable process
However, a new study is putting a damper on this crucial sustainable process. Researchers from the University of Gothenburg investigated recycled plastic pellets gathered from 13 different nations and discovered they contained hundreds of hazardous substances, including pharmaceuticals and pesticides.
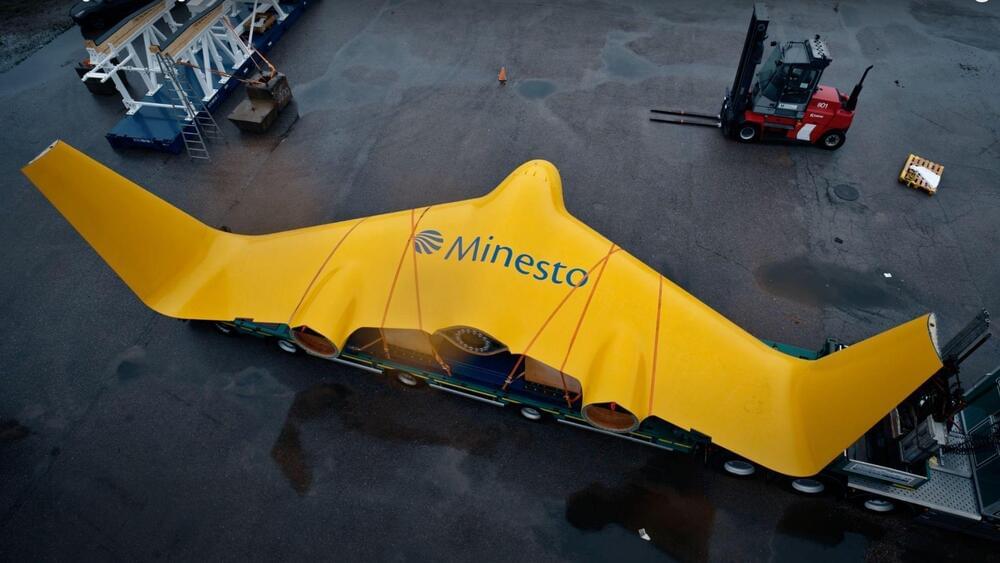
The Evolution of Stretch
Boston Dynamics Starting from the technological building blocks of Atlas, Stretch has the mobility, power, and intelligence to automate warehousing’s toughest tasks. See how we went from initial idea to a product delivering value in the real world.
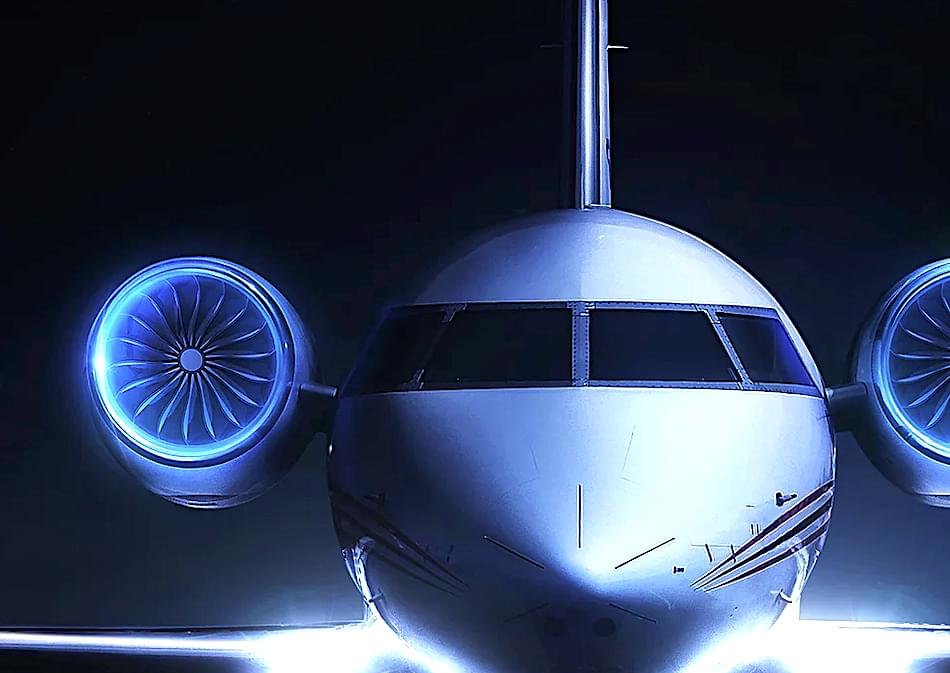
Revolutionary New Electric eJet Motor Could Signal a Breakthrough in Electric Propulsion for Aviation
The aviation industry could be on the cusp of a revolution, following recent tests of a new purely electric jet engine that packs the same punch as its traditional fossil fuel-burning cousins.
Canadian-based company Duxion Motors recently celebrated a significant milestone with the successful ground test of its eJet Motor – the world’s first rim-driven jet propulsion motor.
The eJet motor, an electric jet engine, represents a significant leap in electric aviation, utilizing permanent magnet technology to deliver unprecedented power-to-weight ratios within a compact design. Duxion’s approach could revolutionize the industry, offering scalable efficiency suited to larger aircraft, hybrid cooling for enhanced power density and reliability, and a flexible design that can be tailored to various airframes.
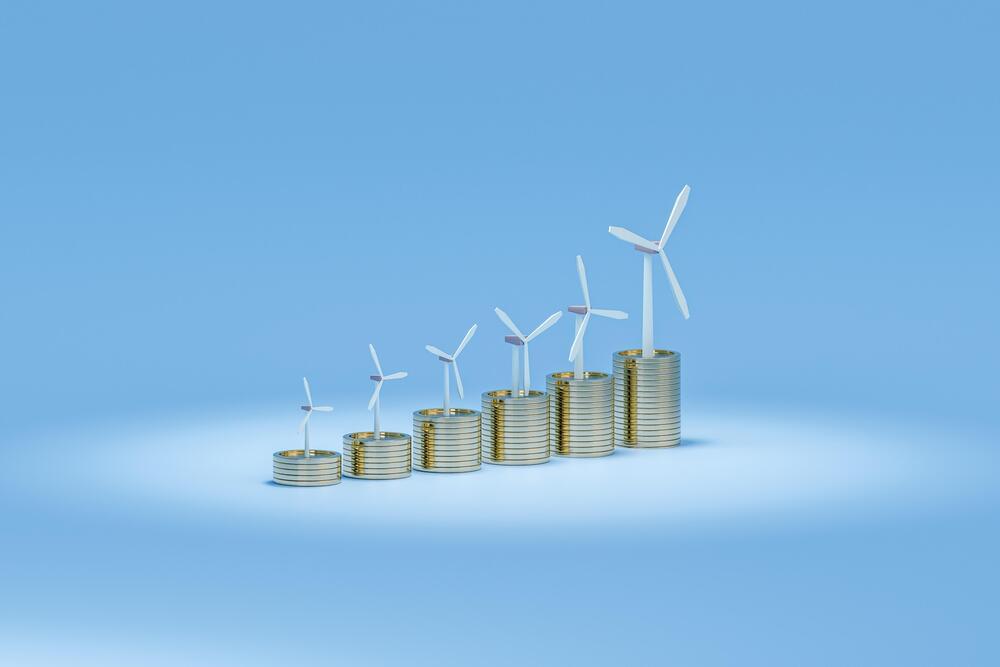
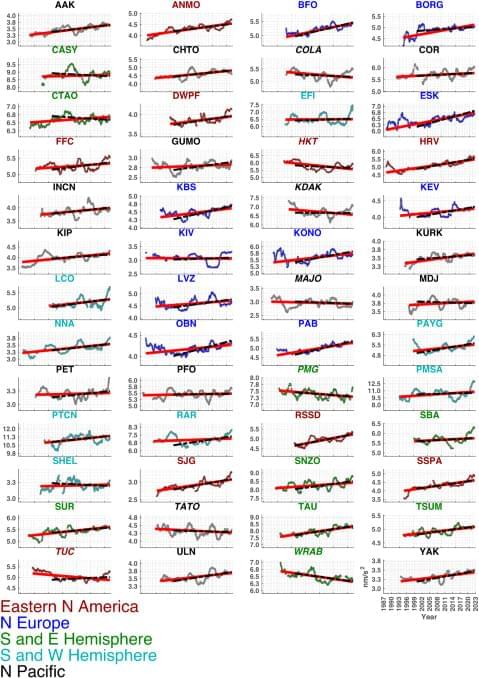